I started the day getting all of the bolts in the bracket holes so I could hang the springs. One thing I had never thought about with a bolt on kit was access to the holes! The two inner holes on each rear bracket had obstacles. On the driver side it was not too bad as there was a small gap I could just fit a finger in to maneuver the bolts in the holes.
The passenger side was another story since the frame rail sits right against the spare tire well. I did the front bolt first so nothing would block the path to the hole. I tied a thread to a zip tie and fished the thread up and out. From there I took the zip tie off and tied the thread to the tip of the bolt. I then pulled the bolt along the rail to the hole and helped it stand up with screwdriver. I stood it up but it did not want to drop down. I got my pry bar and gently placed it on top of the bolt and pushed it through. It worked a lot better than I had hoped. I held it down while starting the nut. Then I fished the wrench in and held the top while tightening up the nut.
For the next hole I used a pair of fishing pliers and maneuvered the bolt over the hole and it dropped right in.
Once everything was tight I bolted the springs and rear back up and put the tires on. Once the tires were on I could let the car back down on it's own weight to check the pinion angle. Looks to be right on the money. Optimal is 3°, 3-6 is acceptable. If your pinion angle is too great the car WILL let you know once you get it up to speed!
Now to check the rear for center. I was off to one side 3/8 of and inch so I needed to push the rear over 3/16ths. Easy right? I jacked it back up on stands and moved the jack around from the side to hold the front of the rear up to protect my pinion angle. If I did not do this, when I loosen the U-bolts the weight of the end would have twisted the rear on the perches. Once i had that secure I removed the tires again and measured out where I needed to be and used a 2x4 and a hammer to tap it to my mark. Put the tires back on an let it back down.
I'm not sure what happened but the only thing I accomplished was to move the offset to the opposite side LOL .. I will try again tomorrow. This time I will leave the tires on wheel I do it so I can take measurements while moving the rear around.
The tricky part with this is there really isn't a reliable reference point. even the lip of the wheel well I am using could be off from the opposite side. My goal is to have about the same distance between the tire and the inner wall of the well. It's a tight fit as is and even a couple 16ths could cause a rub issue. I am leaning towards thinner tires to cut that issue out all together.
One thing I can see is these springs did not make much of a difference in the height of the car. Normally this kit would lower it about 3 inches. I do understand it will settle in after a while but the old weak springs let it sit low already. f those would have been good then I'm sure the car would have sit much higher allowing a more noticeable drop. I can live with it. I can't afford to lower the right way with air bags so I would rather run it high than to do it blocks and cutting coils etc.
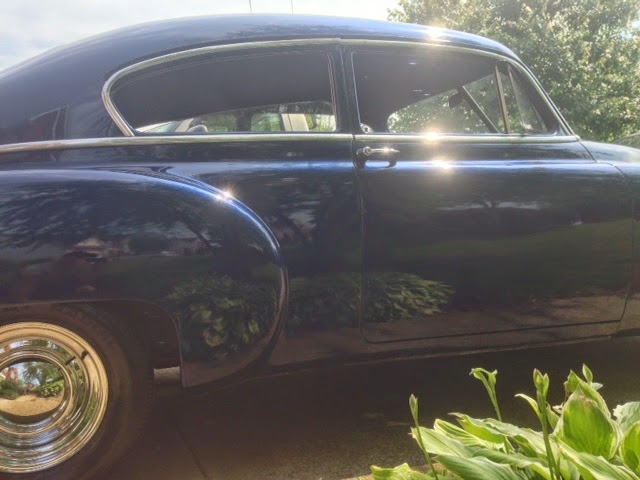 |
Not the best picture for this but this is before. |
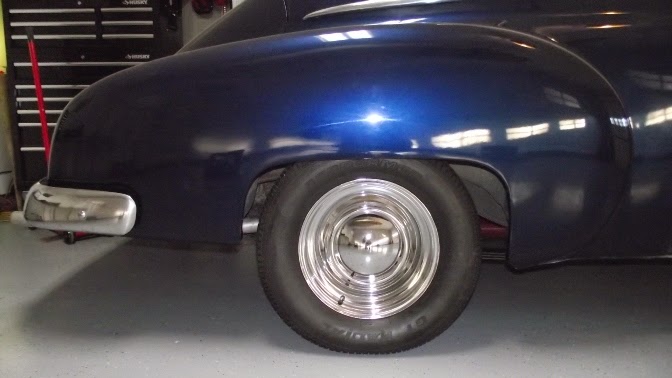 |
After - It may sit higher HA! But it will drop some with time. |
Here's my updated list...
1. I will cut off the original spring pads and grind the area smooth.
2. Locate the mounting position for the new pads. 5-7/16" from brake backing plate
3. Mount the springs onto the axle in approximate location
4. Grind off original driver side spring hangers
5. Put it all back under the car and mark the new hanger locations
6. Mark and drill new holes for the hangers and install.
7. Check and adjust for proper pinion angle
7.2 Adjust the rear for center (side to side)
8. Once in position, spot weld the spring pads.
9. Remove rear and springs for permanent welds
10. Clean and paint
11. Mount rear to car.